Which Syringe Pump and Type of Syringe is Right for My Lab?
Written By: Damon Anderson, PhD
May 06, 2025
The Components, Materials, and Construction Required for Specific Syringe Pump Applications
Syringe pumps play a critical role in biomedical applications. From drug delivery and
molecular discovery to microfluidics and laboratory automation, these precision
instruments ensure accurate and controlled fluid flow.Syringe pumps are indispensable devices for environmental testing, food laboratories,
and more, enabling precise fluid handling for applications such as contaminant analysis,
pesticide residue testing, and microbial detection.Understanding the key components of syringe pumps and the materials used in their
construction ensures optimal performance in specialized applications. Moreover,
reviewing the main components, materials, and their performance capabilities will help
users select the right pump for their specific needs.
Syringe Pump Components
1. Drive Mechanism - At the heart of a syringe pump is the drive mechanism, which controls the linear movement
of the syringe plunger. The three main types of driving mechanisms are:- Stepper Motors: Provide precise and repeatable motion, essential for applications
requiring high accuracy and consistency.
- Servo Motors: Include a built-in feedback mechanism to monitor and control the
position, speed, and torque of the motor shaft. Servo motors precisely control the linear
movement of the syringe plunger, enabling sub-microliter flow control.
- DC Motors with Encoders: Offer smooth operation and feedback control for regulating
flow rates dynamically.
2. Lead Screw and Nut Assembly - This component converts the rotational action of the motor into linear movement,
allowing for precise control of fluid displacement. The pitch and lead of the screw
determine the resolution and speed of the pump. The material choice of this component
can affect precision and longevity and may include:- Stainless Steel (303, 316, and 420): Resistant to corrosion and provides excellent
mechanical strength for continuous operation.
- Brass or Bronze Alloy: Used for lower friction and smooth motion in delicate
testing applications.
3. Syringe Holder and Plunger Clamp - The syringe holder secures the barrel of the syringe, while the plunger clamp ensures
stable movement of the plunger. Adjustable syringe holders accommodate syringes of
various sizes, providing flexibility for different volumes and applications. Materials include:- Aluminum or Stainless Steel: Ensures robustness and resistance to harsh
chemical environments.
- Polycarbonate or ABS Plastics: Lightweight alternatives for compact,
portable syringe pumps.
4. Control System and User Interface - Modern syringe pumps feature digital control systems that allow users to program infusion
rates, volumes, and time intervals. The interface may include:- LCD or Touchscreen Display: Provides real-time monitoring and easy
parameter adjustments.
- Keypad or Rotary Dial Interfaces: Allows manual input for fine-tuning of settings.
- Remote Control: Enables integration with external devices such as laboratory
automation systems and high-throughput instrumentation.
The Fusion 200X Automated Syringe Pump is a large automated two-channel syringe pump with programmable, dual-channel infusion and withdrawal capabilities. This system is equipped with micro-stepper motors and high-precision machined components to handle challenging lab and diagnostic applications.
The Fusion 200X features programmable multi-step mode for complex multi-step flow rates. User access is provided using a glass touchscreen and data can be accessed via USB, RS232, with computer control using LabVIEW, MatLab, and related analysis software. Modular 4-syringe or 11-syringe push/pull rack available. The device holds syringes from 0.5μL to 60mL. Rates from 0.0001 μL/min to 84.7 mL/min, with multiple additional options available.
5. Sensors and Feedback Systems - Advanced syringe pumps incorporate sensors that enhance precision and safety:- Pressure Sensors: Detect and measure the pressure within the syringe and ensure
smooth operation in high-pressure applications.
- Optical Encoders: Provide precise plunger positioning for microfluidic and low-volume
data for analyses.
- Flow Rate Systems: Maintain constant infusion rates despite variations in
fluid viscosity.
6. Power Supply - Syringe pumps operate on various power sources to suit different operating environments:- Standard Power Cords (10A 120 V): Can be used across multiple syringe pumps and
are designed for both domestic and international use.
- AC Power Adapters: Ideal for continuous use in laboratory settings.
- Battery-Powered Models: Offer portability for use in medical settings or for field
testing of water quality and environmental contaminants.
7. Communication Ports - Modern syringe pumps feature communication ports for data logging, automation, and
external control. Common interfaces include:- USB, RS-232, and RS-485 Interfaces: Allow for integration with computers for
advanced programming and laboratory information management systems (LIMS).
- Ethernet and Wi-Fi Connectivity: Enable remote monitoring and operation in
connected environments.
The Fusion 4000X is a motorized, multi-channel syringe infusion pump with dual independent infuse and withdraw channels.This motorized multi-channel syringe infusion pump system is designed for a wide range of biopharmaceutical research like lipid nanoparticles, microfluidic mixing, and lab-on-chip flow control in drug formulation applications. With an all-glass touch screen and precision machined metal design, the Fusion 4000-X dual-channel syringe pump is easy to clean, for lab and GMP environments.
8. Syringe Materials - Biomedical syringes must be constructed from materials that ensure durability and
chemical compatibility. Industrial, environmental, and food testing applications demand
materials that withstand chemical exposure and rigorous cleaning protocols. Common
materials include:- Stainless Steel (304/316 Grade): Provides corrosion resistance, strength, and resistance
to aggressive solvents and decontamination processes.
- Medical-Grade Plastics: Lightweight and compatible with biological fluids.
- Polytetrafluoroethylene (PTFE/Teflon): Excellent chemical resistance for handling
reactive solutions.
- Polyetheretherketone (PEEK): High-performance plastic with superior chemical and
thermal stability.
- Glass Syringes: Used for sensitive applications where plastic could introduce leachables
or absorb trace compounds.
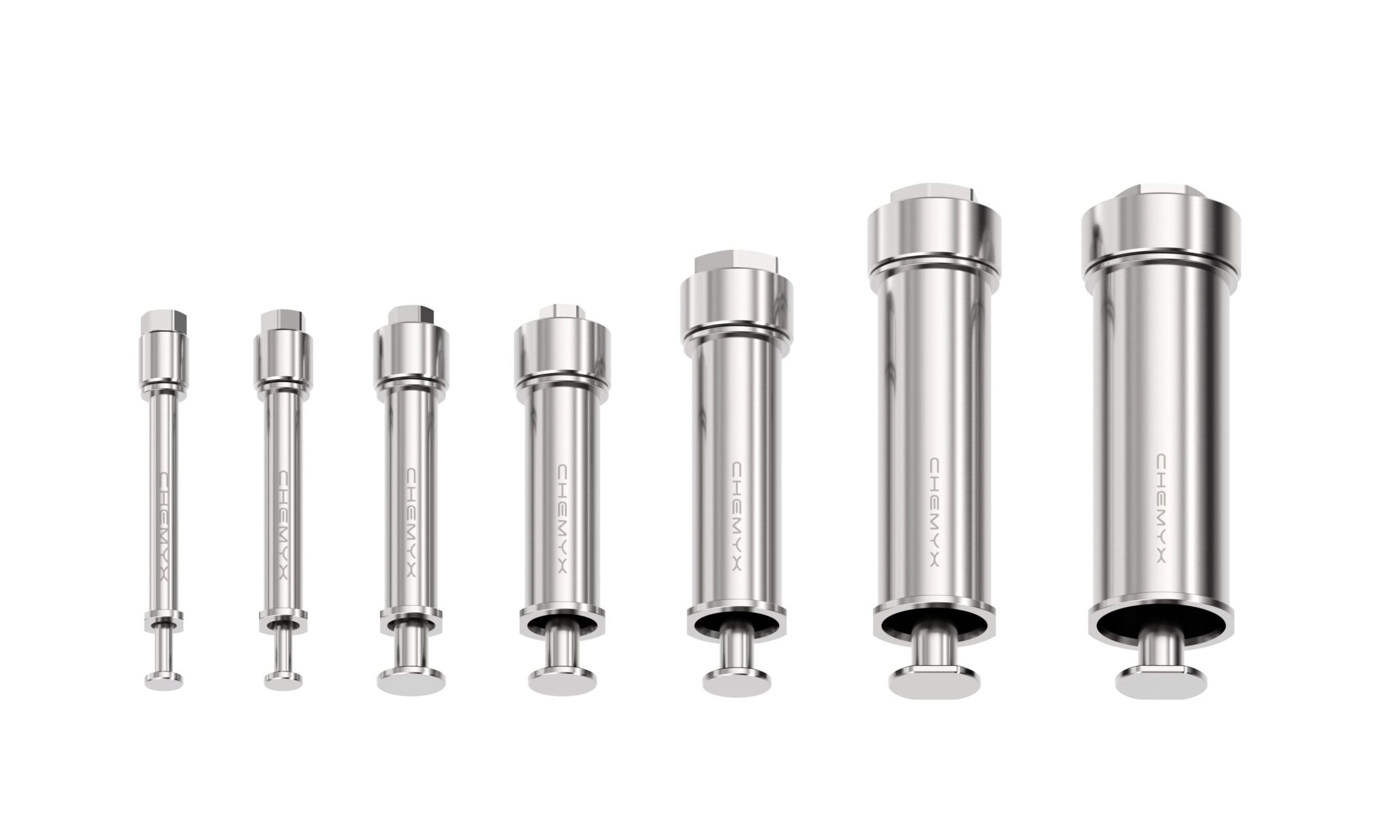
Machined for high-pressure applications, Stainless Steel syringes made of 316 stainless steel are the most powerful available for the Chemyx syringe-pump product line. These precision-machined syringes are resistant to corrosive materials and are best paired with the Fusion 4000-X or Fusion 6000-X high-pressure syringe pumps, which accommodate high-pressure applications. The reusable metal syringes are available in 6, 10, 20, 50, 100, 200, and 300 ml sizes with removable replaceable fitting tips. Available fittings include Genuine SWAGELOK® syringe to tube fittings in 1/16, 1/8 and 1/4 inch sizes and metric sizes 3mm and 6mm. A Luer lock end fitting and hose barb fittings in 1/8 and 1/4 inch sizes are also available. All fitting tips are interchangeable with all syringes (6 to 300 ml) in the series.
9. Material Importance for Specific Applications - Biomedical applications demand specific material properties to ensure safe and efficient
operation. Environmental, industrial, and food testing applications require material
properties to ensure reliability and precision. Below are key material considerations:Chemical Resistance
Certain biomedical and pharmaceutical applications require handling aggressive chemicals and solvents. Materials such as PTFE, PEEK, and stainless steel are essential due to their ability to withstand strong acids, bases, and organic solvents without degradation.Hastelloy C Syringes resist sulfuric acid and nitric acid, while Nitronic 50 Syringes offer resistance to corrosion from salts and chlorides. Hastelloy C and Nitronic Syringes are available in 50mL, 100mL, 300mL, and 400mL volumes.Viscous Liquid
Highly viscous liquids, such as gels and polymer solutions, can be challenging due to high
viscosity and density. Analyzing food products, such as syrups, polysaccharides, oils, and
emulsions requires pumps with strong mechanical components. Stainless steel plungers
and reinforced lead screw assemblies can provide the necessary force and durability to
handle these fluids without clogging or excessive wear.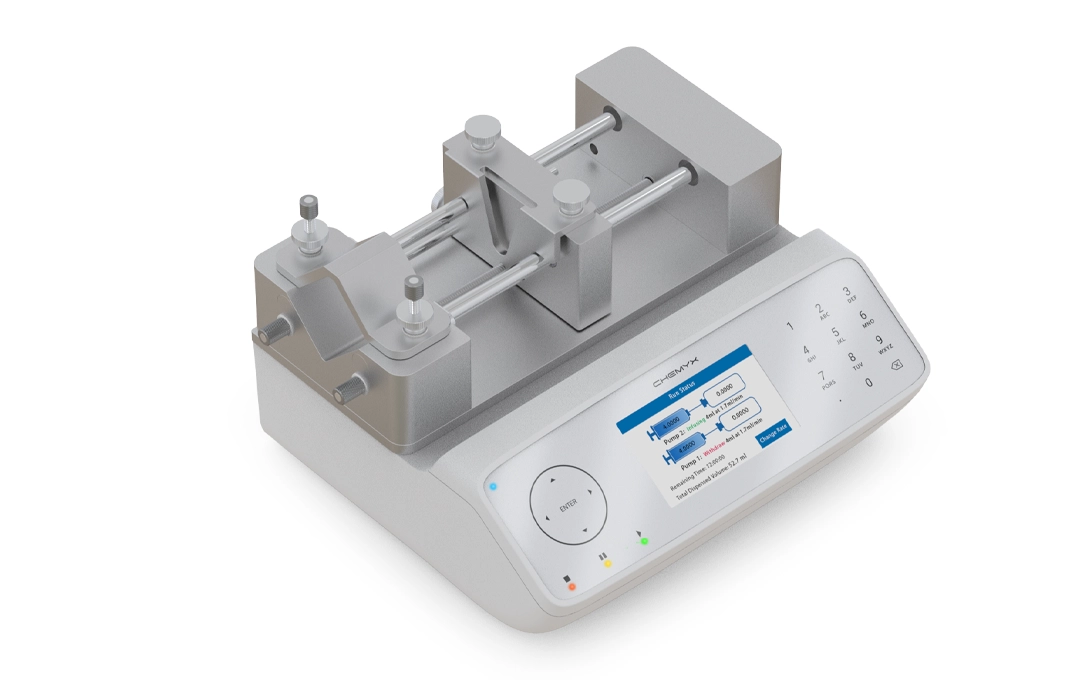
The all-glass touch screen and heavy-duty mechanical structure, allow the Fusion 6000-X constant pressure syringe pump to be easy to clean and has high durability for industrial lab environments.The modular 4 syringe expansion pack increases syringe capacity, using syringes from 5mL to 300 mL with flow rates of 0.0001 mL/min to 408 mL/min. An add on syringe header and/or pressure sensor can provide pressure monitoring and enhanced flow control.Complex Solutions
Biological and pharmaceutical applications often involve solutions with multiple active components, such as proteins, lipids, and suspensions. Materials like medical-grade plastics and glass syringes help maintain the stability and purity of these solutions by minimizing interactions and contamination risks.Industrial and environmental applications involve multi-component solutions, such as wastewater or hydraulic fracking samples, where particulates and organic compounds can interfere with fluid handling. Corrosion resistant and chemically inert syringe barrels minimize contamination risks while maintaining sample integrity.High-Pressure Applications
Certain applications, such as high-performance liquid chromatography (HPLC), high pressure drug infusion, and high-pressure liquid extractions, require syringe pumps that can withstand significant pressure. Stainless steel components offer excellent mechanical strength, ensuring consistent performance under high-pressure conditions.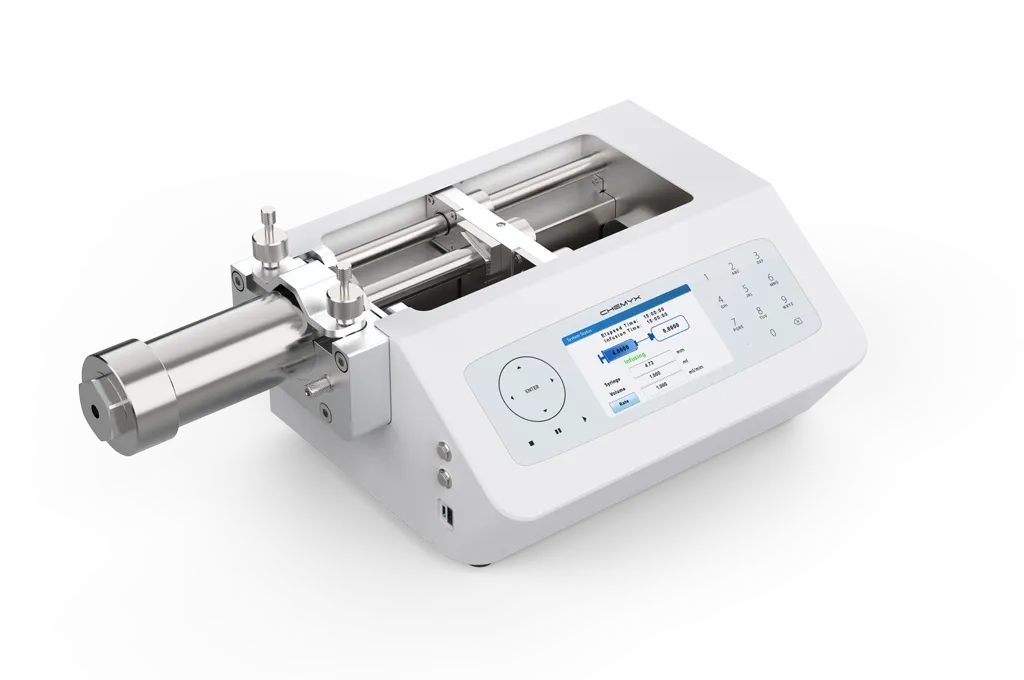
The Chemyx HP1 is a heavy-duty high-pressure syringe pump designed for elevated pressures in research, industrial, and manufacturing applications.This specialized high-pressure syringe pump is designed for demanding conditions associated with supercritical fluids, hydraulic fracturing, and nano-encapsulation which exist at temperatures and pressures beyond their critical points.The HP1 high-pressure syringe pump is engineered with materials and components that can withstand challenging conditions often at pressures exceeding 10,000 psi, including heavy-duty drive shafts, high-performance drive transmission, and corrosion-resistant metal enclosure.Additionally, the Hp1 high pressure syringe pump has optional pressure detection and syringe heaters for additional experimental condition control in materials science, pharmaceuticals, and environmental process analysis.Conclusion
Syringe pumps are essential tools in biomedical applications, requiring precision, reliability, and flexibility. Understanding their components and material properties helps researchers and clinical professionals select the right pump for their specific needs, ensuring accurate and efficient fluid handling in various settings. Syringe pumps are also essential for precision fluid handling in environmental and food testing applications. Their reliability, chemical compatibility, and adaptability make them critical for ensuring accurate contaminant detection, quality control, and
regulatory compliance.As technology advances, modern syringe pumps will continue to integrate more innovative controls and improved materials. By selecting the appropriate materials and components, laboratories can optimize syringe pump performance, ensuring robust and reproducible results in various analytical workflows.Published in partnership with Chemyx